- Our Solutions:
- Air Floating Solutions for Defect Inspection (AOI) Systems
- Wafer Backside Contamination
- Air Floating Solutions for OLED InkJet Printing Systems
- Air Floating Solutions for Photoresist Coating Systems
- Air-Floating Solutions for UV Curing Systems
- Ultra-Thin Wafer Handling
- Warped Wafer Handling End Effector
Innovative handling solutions to accelerate performance and improve quality & yield
- Our Solutions:
We offer our customers, high innovative system solutions for demanding applications
- Our Solutions:
CoreFlow offers innovative wafers handling solutions for the Semiconductors industry. Our solutions enhance the Production Yield, provide High Precision, and better Throughput.
By focusing on the critical challenges in silicon wafers handling within the semiconductors process, our solutions:
- Eliminate the risk of wafer backside contamination
- Ensure maximum optimization of handling warped, thin, and flexible wafers.
- Strong vacuum grip with partially covered pads
Explore our air-flow solution could be integrated into inspection, metrology, and other semiconductor process systems, providing consistent and reliable handling of wafers with no contact neither at the back nor front side:
Non-Contact Chuck
CoreFlow's Non-Contact Chuck addresses the challenges of reducing backside contamination and handling thin and flexible wafers read more >>
Selective Vacuum
The selective vacuum solution addresses the challenges of handling warped wafers. Utilizing its SmartNozzle® technology, The handling mechanism acquires the wafer read more>>
Robot End Effector
CoreFlow’s End Effector (EE) family addresses the challenges of handling all types of wafers, including thin, perforated, compound, glass, bare and polish wafers ... read more
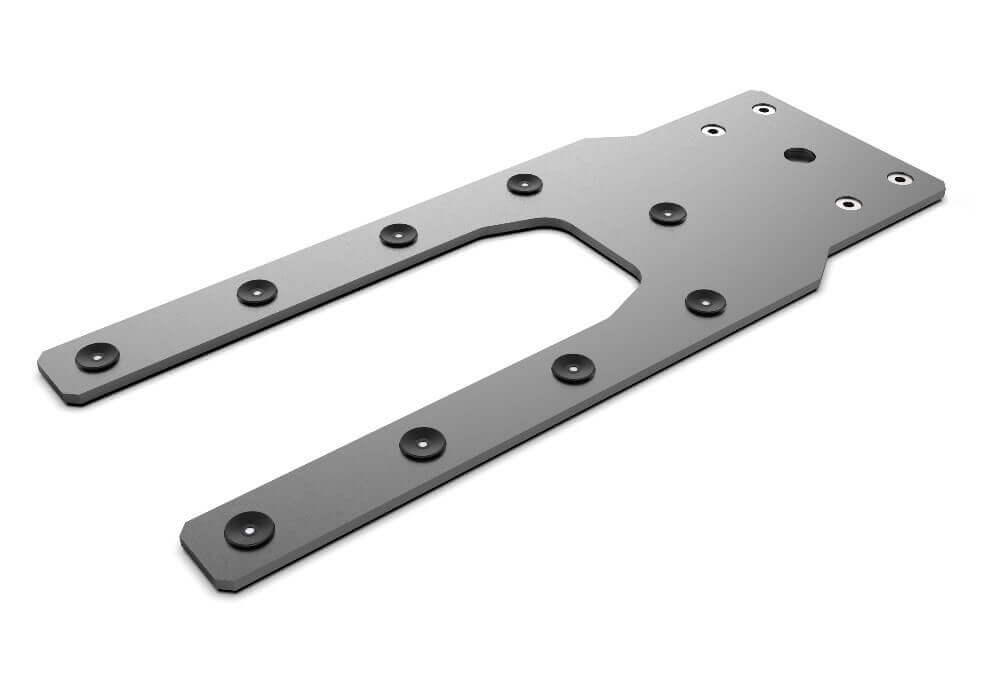
- Our Solutions:
Thank you for contacting us!
Your details were sent successfully.
Our representatives will be in touch with you shortly.
CoreFlow team
- Our Solutions:
Be a world class leader of innovative, high performance aeromechanical
solutions for the flat panel display, semiconductor
and other industries
- Our Solutions:
- Short Text:
Motion Systems
CoreFlow’s aeromechanical solutions for fab automation enable the conveying and handling of substrates with minimal contact between the substrate and the conveyor, preserving the quality of the substrate while minimizing Total Average Cycle Time (TACT).
CoreFlow’s motion systems perform loading, unloading, conveying, flip-over, and gripping actions on substrates of all weights and sizes, with precise positioning. Multiple mounting and configuration options ensure that CoreFlow solutions fit accurately and economically into any manufacturing line.
The motion systems solutions combine configurable air bars and advanced motion systems such as Vacuum Pre-Loaded (VPL) and V-wheels.
- Our Solutions:
- Short Text:
Semiconductor devices are the beating heart of almost every electronic product. These devices rely on the electronic properties of semiconductor material. The devices are manufactured both as single discrete components and as ICs that integrate millions or even billions of transistors (!), manufactured and interconnected on a single semiconductor wafer (also known as a substrate). The constantly increasing demand for more computing power and memory on smaller devices, and a lower rate of energy consumption, drives the wafer manufacturing process to the limit. Sensitivity to process cleanliness drives efforts to achieve particle reduction, while the push for thinner substrates has led to increased levels of warping – and new challenges in wafer handling.
CoreFlow addresses these challenges by providing non-contact chucks that handles semiconductor wafers without any contact, and selective vacuum products that are specifically designed to handle warped and/or odd shape wafers.
CoreFlow’s non-contact and selective vacuum products are adopted by major semiconductor equipment manufacturers in three different continents.
The constantly increasing demand in the semiconductor industry, for more computing power and memory on smaller devices, and a lower rate of energy consumption drives the wafer manufacturing process to the limit. Sensitivity to process cleanliness drives efforts to achieve particle reduction, while the push for thinner substrates has led to increased levels of substrates warping – and new challenges in wafer handling.
Driven by the extreme purity requirements of wafer handling, CoreFlow addresses the challenges of reducing wafer backside contamination. Utilizing its unique aeromechanical technology, CoreFlow’s non-contact chuck safely handles semiconductor wafers, applying pressure and vacuum forces that flatten the wafer and keep it hovering at a micron over the chuck’s surface.
CoreFlow’s selective vacuum (SV) technology was developed specifically for the handling of warped and/or odd-shaped wafers. The vacuum adapts itself to the wafer surface, ensuring safe, non-contact handling, thereby improving manufacturing yields.
CoreFlow’s non-contact chuck and Selective Vacuum products have been adopted by major semiconductor equipment manufacturers on three different continents.
- Our Solutions:
- Short Text:
The Flat Panel Displays are thin and lightweight display screens that are used in laptops, monitors, televisions, smartphones, digital cameras, and other portable devices. Flat-panel size requirement varies as per the end device on which it is mounted. With the introduction of more innovative technology-based solutions, flat panel displays can be found in the majority of consumer and industrial display systems.
Today flat panel displays mostly use LCD (liquid crystal display) technology but in recent years there is a shift toward the use of the organic light-emitting diode display (OLED) technology which is gaining large momentum. OLED displays are not just thinner and more efficient than LCD displays - they provide superior image quality and they can also be made transparent, flexible, foldable, rollable, and stretchable.
Driven by end-user demands for increased product quality and lower costs, FPD manufacturers are constantly searching for improved processes and fab automation equipment. In addition, larger (G8 to G11) and thinner glass (<0.4mm) substrates are more complex to process and present ongoing precision and handling challenges for equipment manufacturers.
CoreFlow addresses these challenges by providing high-performance floating solutions that handle and convey glass substrates of any size and weight with maximum reliability, precise Z positioning, glass flatness, and with minimal maintenance requirements. Our solutions are used by many leading fabs worldwide.
Driven by end-user demands for improved product quality and reduced costs, FPD manufacturers are constantly on the lookout for new, state-of-the-art process and fabrication automation systems. In addition, larger, thinner glass substrates and more complex processes present ongoing precision and handling challenges for equipment manufacturers.
CoreFlow addresses these challenges by providing high-performance aeromechanical solutions that handle and convey glass substrates of any size and thickness with maximum reliability, offer precise Z-axis air-gap positioning, and provide optimal substrate flatness – with minimal maintenance requirements. Our solutions are used by many leading fabs in Korea, Taiwan, Japan, China, North America, and Europe.
- Our Solutions:
Be a world-class leader of innovative, high performance aeromechanical
solutions for the flat panel display, semiconductor, and other industries
CoreFlow will invest efforts in order to maintain its market leadership position while:
- Generating profits from its revenue and operation
- Investing in R&D in order to ensure continuing growth
- Fostering innovative activity according to the potential and risk strategy
CoreFlow shall explore new additional applications where its technology can bring commercialized added value, in order to open more opportunities for future growth and risk reduction.
CoreFlow shall implement the following HR strategy:
- Sustaining a learning organization
- Creating a rewarding and empowering work environment
- Our Solutions:
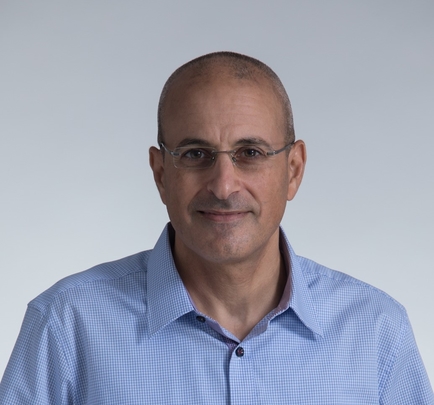
Alon Segal, CEO and VP R&D
Alon Joined CoreFlow in 2016 as VP of R&D and in May 2023 appointed as CEO. Alon brings vast experience with global organizations spanning various R&D leadership positions, project management, and the development of multi-disciplinary systems. Before joining CoreFlow, Alon worked at Carestream Health in various technical R&D leadership roles and as Technical Program Manager (TPM) in the medical space arena. Prior to joining Carestream, Alon served as a project manager for electro-optical equipment at CI Systems and as the mechanical department manager at ADT for the semiconductor industry.
Alon holds a B.Sc. in Mechanical Engineering from Technion Israel an MBA from the University of Haifa and is Project Management Professional (PMP) certified by the Project Management Institute (PMI) Organization.
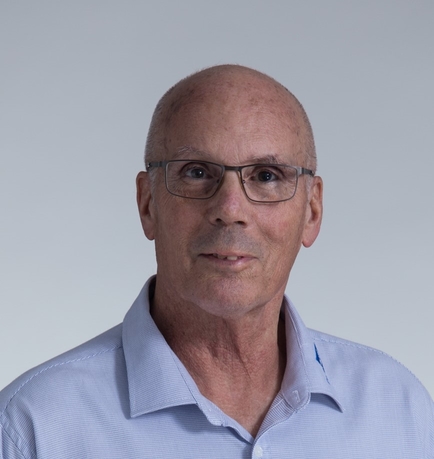
Dr. Boaz Nishri, CTO
Boaz joined CoreFlow as CTO in 2007. Previously, Boaz was VP R&D at CorAssist Ltd. and CTO at MindGuard Ltd - both medical device companies. Boaz was a research associate at Tel Aviv University Faculty of Engineering, where he supervised experimental research on aerodynamics.
Boaz holds an MA and Ph.D. in engineering from Tel Aviv University, where he carried out research and wrote a software program for the Aerodynamics Laboratory for air velocity measurements in a turbulent flow.
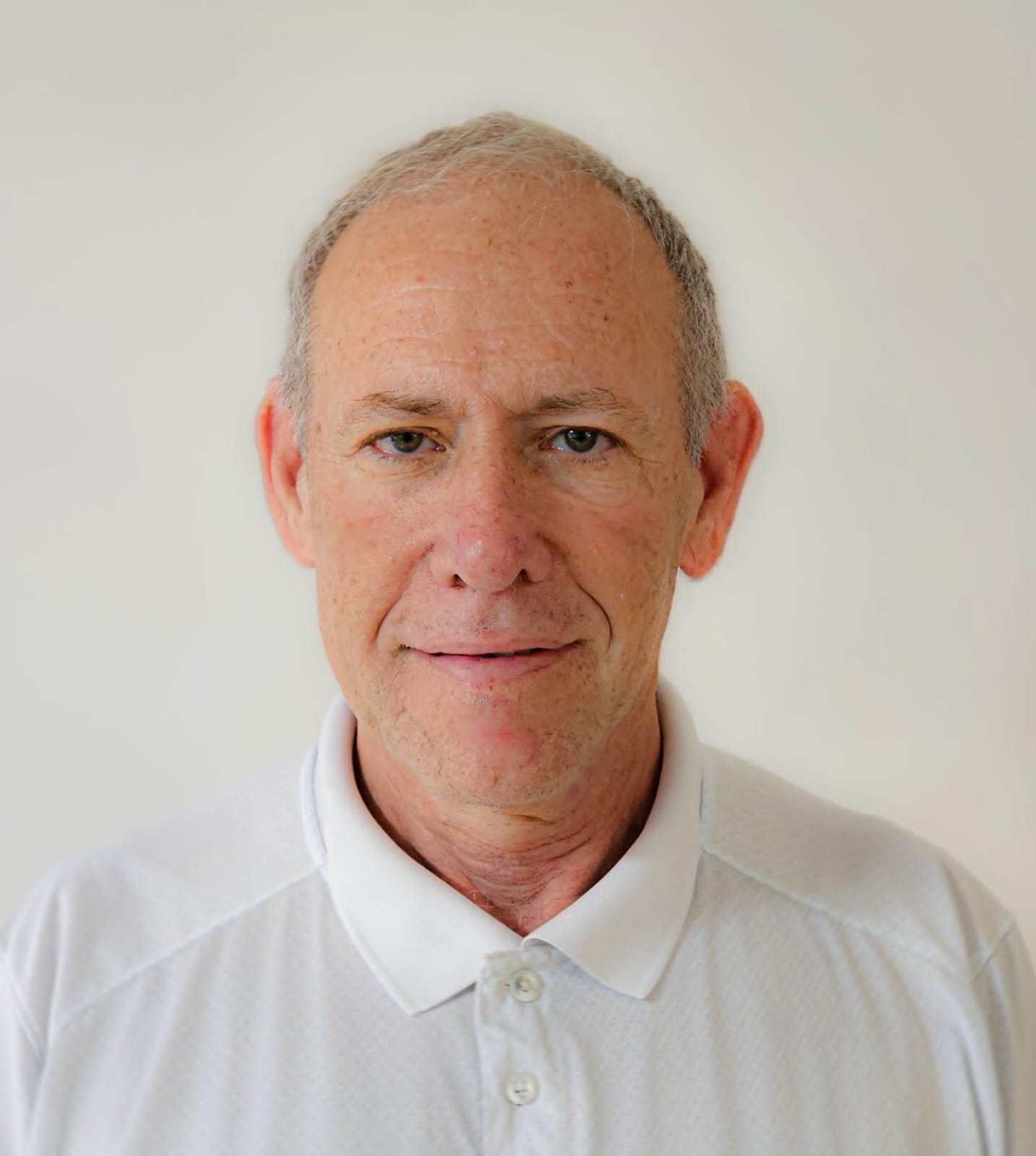
Alon Kapel, VP Sales & Marketing
Alon Kapel joined CoreFlow in late 2023 as VP of Sales & Marketing.
Mr. Kapel brings a wealth of global sales and marketing experience in multidisciplinary systems, having held senior positions at renowned companies such as CNOGA Medical, Jordan Valley X-Ray Metrology (Bruker), and Chip Express.
Alon began his career as a Semiconductor Process Engineer, mastering Dry Etch, CVD, and PVD processes at National Semiconductors fabs in Salt Lake City, UT, and in Fab1 in Migdal HaEmek Israel. He also gained valuable experience in ASIC production supply chain management as well as experience in X-ray metrology equipment sales for advanced semiconductor fabs.
Alon holds a B.Sc. in Chemical Engineering and an MBA from the Technion, Israel Institute of Technology.
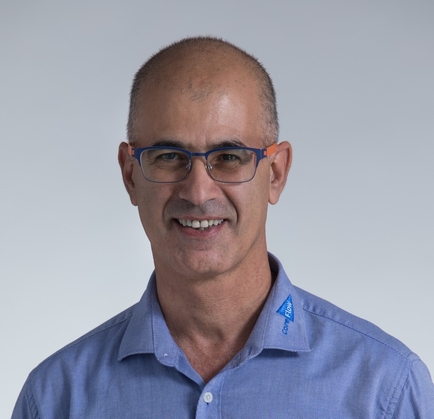
Asher Shlush, VP of Operations
Asher joined CoreFlow at the end of 2014 as Operations Manager and in December 2015 was appointed to Factory Executive. Previously, Asher was employed as a production manager at Caesar Stone, development manager, sourcing manager, and knitting manager at Delta Textile.
Asher graduated as a Practical Engineer in industrial engineering from Braude College, Israel.
- Our Solutions:
CoreFlow develops, manufactures, and markets advanced handling and conveying solutions, for Flat Panel Display (FPD) and Semiconductor equipment manufacturers. With more than 800 installations worldwide, CoreFlow’s air floating solutions can be found in the production floors of many top FPD manufacturing fab plants, where they reliably handle the glass panels of the leading display manufacturers.
CoreFlow’s non-contact air floating solutions transport glass substrates of any size, thickness, and weight (including the latest G10.5 and 0.1 mm), between and within process systems with the utmost air-gap accuracy.
CoreFlow innovative aeromechanical solutions address the challenges of reducing backside contamination and handling warped wafers, for various applications within the Semiconductor process, and other industries.
CoreFlow brings several decades of combined aeromechanical expertise to deliver manufacturing solutions with unmatched quality, accuracy, and stability – solutions that minimize your risk and maximize your manufacturing yield and throughput.
CoreFlow’s headquarters and research facility is based in Israel, with sales representatives located in Korea, Japan, Taiwan, China, and Germany.
>> Click here for company profile video <<